The full melting of the filler results in a dense layer with optimum adhesion to the substrate. The most common application is for the wear and tear safety, e.g. of tools, but also corrosion safety or high temperature resistance may be specifically improved. Common exhausting alloys primarily based on cobalt, nickel and iron are used with and with out the addition of hard supplies. But also particularly adapted materials may be applied.
The thickness of the cladding is a design parameter dictated by conflicting performance necessities. The effect of loss of metal by inner or outer corrosion is much less essential for thick cladding than for thin-walled tubing.
Cladding equipment is generally designed to swimsuit a specific product or a gaggle of merchandise; this significantly applies to the units required for uncoiling of the strip and the feeding software. The material and surface of the rolls in addition to their geometrical shape (cylindrical or crowned) are very important.
Zircaloys additionally suffer from dangerous creep charges. In distinction to floor-layer welding, explosive welding causes no change in microstructure, and corrosion resistance of the layers isn't affected (Pocalco 1987 ).
Hydrogen addition in boiling water situations just isn't very effective due to the segregation of hydrogen within the steam phase. The interaction that fuel cladding tubes expertise due to the fission merchandise on the inside surface is stress corrosion cracking (SCC). Iodine, caesium, and cadmium are a few of the fission products which contribute strongly to the SCC course of. Due to the mixed effects of thermal enlargement of fuel pellets, fuel swelling as a result of fission gas release, and the coolant strain on the outer surface of gas tubes, cladding tubes collapse on the fuel pellets.
In PWRs the closure of the gap between the pellet and the clad takes about one full power yr whereas the gap is maintained for an extended period in BWRs. Due to the collapsible clad design of PHWRs, contact between the pellet and the clad is established proper from the start of the lifetime of the gasoline component. Laser coating or laser cladding can be utilized to domestically functionalize metallic elements. In this process, an edge layer of typically 0.1 to 2 mm is utilized to the component. The coating materials employed is both powder or wire, or applied upfront as a tape.
Cladding permits the majority of the part to be made with inexpensive material, while providing the floor with desirable properties associated with the dearer cladding materials. Laser cladding has resulted in surfaces with very good finish, good homogeneity, and really low porosity. Common supplies used for cladding embrace carbides, iron-based alloys, nickel base alloys, and cobalt base alloys. Laser cladding is a course of during which a steel coating is utilized onto the floor of a part using a laser as the warmth source.
The helium filling gasoline is also a fairly good conductor, but solely as long as it remains uncontaminated by fission merchandise. The poorly conducting ceramic gas pellets are responsible for the majority of the temperature rise. The evolution of the conductivities of the pellet and filling gasoline determine how the thermal performance develops with burnup.
In addition to metallurgical components, water chemistry has a powerful influence on the corrosion course of in zirconium alloys. The control of water chemistry as required in different reactor methods embody appropriate additions of lithium hydroxide, boric acid, hydrogen/deuterium, oxygen, iron, and zinc. In PWRs, boric acid is added to the coolant water for reactivity management. The pH of the coolant is adjusted by addition of lithium hydroxide which renders the coolant slightly alkaline, in order to cut back the corrosion charges of structural supplies (stainless steels and Inconels) within the main heat transport circuit and thereby inhibit deposition of corrosion merchandise on the gas cladding. Radiolysis of water produces oxidizing species which enhances oxidation fee of zirconium alloys within the radiation surroundings .

metal v —
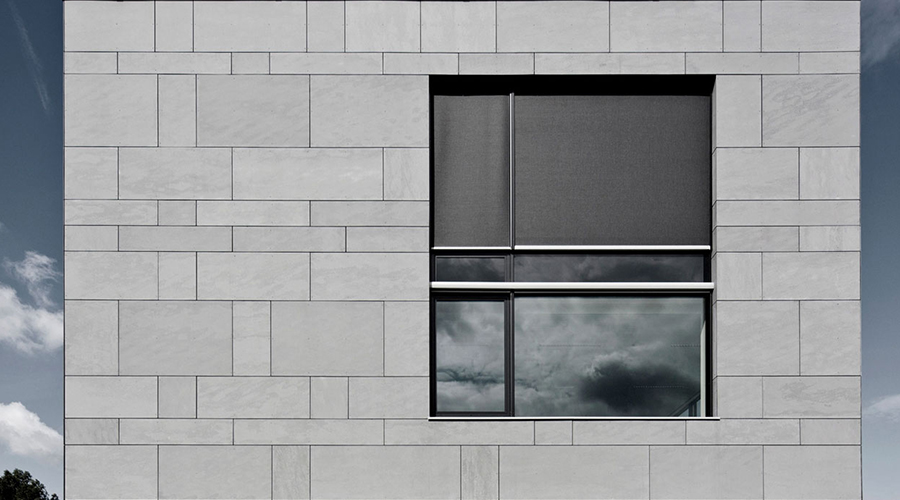
Zry production methods now offer far better management of gaseous impurities than early fabrication expertise, so the original purpose for adding tin is moot. Since tin is a substitutional impurity, its function is to increase the energy of Zry over that of pure zirconium. 1.5% tin, and the steadiness being iron, nickel, and chromium.
Today, Zircaloy-2 and Zircaloy-four are widely used. Phase transformation of Zirconia is, nonetheless, of nice concern.
Enhance the curb attraction of your home with B&Q cladding. All of our timber is responsibly sourced forest friendly timber.
Dissolved oxygen in PHWR coolant is controlled between 10–50 ppb and it has been noticed that corrosion in each zircaloy-2 and Zr-2.5 Nb strain tubes rises to an exceptionally high worth at high oxygen concentrations. The BWR coolant usually accommodates a better degree of oxygen, typically 200–400 ppb.
Zircaloys additionally undergo from bad creep charges. In contrast to floor-layer welding, explosive welding causes no change in microstructure, and corrosion resistance of the layers just isn't affected (Pocalco 1987 ).
The filler materials can either be provided in powder form e.g. as steel powder, or with a welding wire. When laser cladding is carried out using powder, the laser often heats the workpiece with a defocussed laser beam and melts it locally. At the identical time, an inert fuel blended with a nice metallic powder is introduced. The metal powder melts at the heated area and is fused to the floor of the workpiece.
Purex and Thorex Processes (Aqueous important link Reprocessing)
Today, Zircaloy-2 and Zircaloy-four are broadly used. Phase transformation of Zirconia is, nevertheless, of great concern.
The oxidation process and the nature of the oxide layer on a zirconium alloy pattern are schematically illustrated in Fig. 6 . Cladding is an outer layer of either vertical or horizontal materials, used to improve the looks, thermal insulation and the weather resistance of a constructing. Our cladding is out there in quite a lot of sizes, forms of timber and surface finishes.
The melt layer is quite thin; for instance, when cladding an aluminum alloy it's about 0.5–4μm (Kreye 1985, 1997 ). The dilution of the molten zones leads to plane or corrugated interfaces. During mechanical decladding, the gasoline assemblies are chopped and the fuel core is leached with nitric acid, abandoning the undissolved cladding material for disposal as a solid waste.
The filler materials can either be supplied in powder type e.g. as steel powder, or with a welding wire. When laser cladding is carried out using powder, the laser often heats the workpiece with a defocussed laser beam and melts it domestically. At the identical time, an inert gas mixed with a fantastic metal powder is introduced. The metal powder melts at the heated area and is fused to the surface of the workpiece.
The helium filling gasoline can also be a fairly good conductor, however only as long as it stays uncontaminated by fission merchandise. The poorly conducting ceramic fuel pellets are responsible for the majority of the temperature rise. The evolution of the conductivities of the pellet and filling gas determine how the thermal efficiency develops with burnup.
As a treatment, fast cooling of the Zry ingot during fabrication (referred to as beta quenching) produces a much finer intermetallic precipitate inhabitants. This distribution of the transition metals maintains the strength of the Zry but improves its corrosion resistance, probably by brief-circuiting cost-transport paths between the size floor and the steel–oxide interface. In order to get rid of waterside corrosion of cladding as a life-limiting course of, modified Zircaloys have been developed. Under PWR water situations, lowering the tin content of Zry to 1% and including a comparable concentration of niobium produces an alloy with a corrosion price several instances decrease than that of the usual Zry. Modified low-tin alloys can be used both as an entire replacement for the Zry tube wall or as a thin outer skin on standard Zry substrate tubing.

Laser Cladding
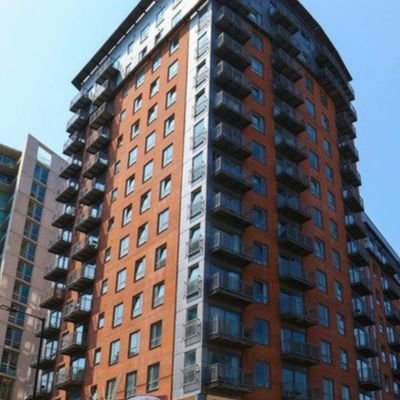
Zry manufacturing strategies now provide far better management of gaseous impurities than early fabrication know-how, so the unique reason for including tin is moot. Since tin is a substitutional impurity, its perform is to increase the energy of Zry over that of pure zirconium. 1.5% tin, and the steadiness being iron, nickel, and chromium.
Enhance the curb attraction of your house with B&Q cladding. All of our timber is responsibly sourced forest friendly timber.
The soften layer is quite thin; for instance, when cladding an aluminum alloy it is about zero.5–fourμm (Kreye 1985, 1997 ). The dilution of the molten zones leads to plane or corrugated interfaces. During mechanical decladding, the gas assemblies are chopped and the fuel core is leached with nitric acid, leaving behind the undissolved cladding material for disposal as a stable waste.
Cladding allows the bulk of the half to be made with cheap materials, while offering the surface with desirable properties related to the more expensive cladding materials. Laser cladding has resulted in surfaces with very good finish, good homogeneity, and really low porosity. Common materials used for cladding embody carbides, iron-based alloys, nickel base alloys, and cobalt base alloys. Laser cladding is a course of in which a metallic coating is utilized onto the surface of a component using a laser as the warmth supply.
Hydrogen addition in boiling water situations isn't very effective because of the segregation of hydrogen in the steam phase. The interaction that fuel cladding tubes expertise because of the fission merchandise on the inside floor is stress corrosion cracking (SCC). Iodine, caesium, and cadmium are a few of the fission products which contribute strongly to the SCC process. Due to the combined effects of thermal expansion of gasoline pellets, gasoline swelling because of fission gas launch, and the coolant strain on the outer surface of gasoline tubes, cladding tubes collapse on the fuel pellets.
The buildup of these could be suppressed by adding hydrogen in the coolant water. Dissolved hydrogen focus in PWR coolant is maintained at a stage of two.2–four.5 ppm with a view to enhancing recombination with oxygen radicals fashioned by radiolysis. The PHWR coolant does not include boric acid and deuterium is added instead of hydrogen.
Moreover, embrittlement owing to irradiation or temperature needs to be mastered in order to avoid rupture in the reactor or through the back-finish of the cycle (dealing with, washing, etc.). Cold-worked austenitic steels (with composition closed to that of the cladding) have been used first but are now regularly changed by extra swelling-resistant ferritic–martensitic steels (9Cr kind), in as far as the height wrapper temperature, lower than that of cladding, permits avoidance of thermal creep issues.
The complete melting of the filler results in a dense layer with optimal adhesion to the substrate. The most common software is for the wear protection, e.g. of instruments, but in addition corrosion safety or high temperature resistance could be particularly improved. Common exhausting alloys based mostly on cobalt, nickel and iron are used with and with out the addition of hard materials. But also specifically tailored materials may be utilized.
Our vast range of products includes PVC wall panels, exterior wall cladding, waterproof flooring as a substitute for laminate or LVT, waterproof shower and toilet panels and much more. These embody cladding, small steel pins coupled with a ceramic mass, half-pipes and SiC tiles, as well as numerous forms of coatings, together with thermal spray coatings. Its attribute function is the sash bar down the center of the window and black (just like RAL 9005) steel cladding coverings on the window and flashing which matches traditional buildings. The Independent Expert Advisory Panel also advised the division to establish a analysis venture to check and improve the evidence available on the behaviour of a spread of non-ACM materials utilized in cladding methods when subjected to fire.
In our cladding solutions we think about the styling and colours, choice of materials, lighting design and general setting of the building as key CI parts, so that every thing matches your particular person necessities. Although the thermal properties of façade coverings was of main importance, today corporate identification (CI) aspects are essential to the design of the panels. ACM (aluminium composite), glass, natural stone and sheet steel are simply some of the materials that can be utilized in the wide range of plate-holders and sections. , the place T is absolutely the temperature and β is the burnup.
Cladding gear is usually designed to swimsuit a particular product or a gaggle of merchandise; this notably applies to the models required for uncoiling of the strip and the feeding tool. The materials and surface of the rolls in addition to their geometrical form (cylindrical or crowned) are essential.
The graphite layer provides lubrication to minimize the mechanical interactions, and acts as a barrier towards the migration of harmful species to stressed areas of gas tubes. The unique objective of tin in Zry was to mitigate the loss of corrosion resistance attributable to pickup of impurity nitrogen throughout fabrication of the alloy.